黑帽快排域名池|【唯一TG:@heimifeng8】|XSS跨站快排技术✨谷歌搜索留痕排名,史上最强SEO技术,20年谷歌SEO经验大佬✨“Hyperadaptor”: South Korea’s super metal that defies heat and cold
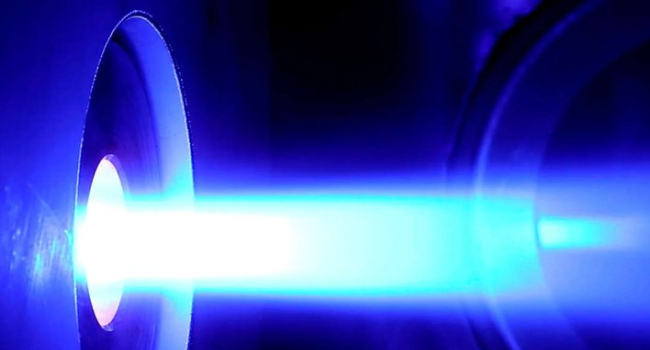
“Hyperadaptor”: South Korea’s super metal that defies heat and 黑帽快排域名池cold
April 21, 2025 19:14Scientists at South Korea’s Pohang University of Science and Technology (POSTECH) have developed a groundbreaking alloy dubbed the “Hyperadaptor.” This material retains its strength and flexibility across an extreme temperature range—from a frigid −196°C, akin to outer space, to a scorching 600°C, as found in turbines. Published in Material Research Letters, this discovery promises to transform the aerospace, energy, and automotive industries. Here’s how this super metal works, what makes it unique, and where it will be applied.
What Is the Hyperadaptor?
The Hyperadaptor is a nickel-based high-entropy alloy (HEA) that combines multiple metals—nickel, cobalt, chromium, and others—in near-equal proportions. HEAs are known for their resilience, but the Hyperadaptor stands out for maintaining mechanical properties—strength, ductility, and deformation resistance—from −196°C (liquid nitrogen temperatures) to 600°C (jet engine heat). It’s the first metal to preserve its characteristics across such a vast range.
Its secret lies in its structure: nanoscale L1₂ particles, just a few nanometers in size, are uniformly distributed within the alloy. These act as a “reinforcing framework,” preventing cracks and deformation. When heated or cooled, the alloy’s structure adapts, ensuring stability. This solves a long-standing issue with conventional alloys, which become brittle in extreme cold or lose strength in intense heat.
Why Is It a Breakthrough?
Traditional metals struggle with extreme temperatures. For instance, steel hardens and cracks at −100°C, while aluminum alloys soften above 400°C. Titanium alloys, used in aviation, withstand up to 550°C but are costly and complex to produce. The Hyperadaptor shatters these limitations:
- Versatility: Performs reliably at −196°C (space or cryogenic systems) and 600°C (exhaust systems, turbines).
- Strength: Retains up to 95% of its mechanical properties in tests, compared to 20–50% losses in conventional alloys.
- Simplicity: While HEAs are complex, POSTECH optimized the composition to reduce costs.
For comparison, invar (an iron-nickel alloy) resists thermal expansion but is brittle in cold. The Hyperadaptor overcomes these constraints, paving the way for durable components.
Where Will the Hyperadaptor Be Used?
Dubbed a “material of the future” for its versatility, the Hyperadaptor has wide-ranging applications:
- Aerospace: Rocket skins, engine nozzles, and heat shields that endure swings from space’s vacuum (−270°C) to atmospheric reentry plasma (up to 2,000°C with insulation).
- Energy: Turbine blades in power plants operating at 600–700°C and cryogenic tanks for hydrogen storage.
- Automotive: Exhaust systems running at 500–600°C and lightweight, robust parts for electric vehicles.
- Industry: Pipelines for chemical plants and offshore platforms, where corrosion resistance is critical.
- Space Missions: Equipment for lunar or Martian bases, facing daytime highs of 120°C and nighttime lows of −150°C.
In China’s “city of the future,” Xiong’an, HEAs are already being tested for smart infrastructure, and the Hyperadaptor could play a role in such projects. It’s ideal for pipelines in extreme climates, like Siberia or UAE deserts.
How Was the Super Metal Created?
Led by Professor Hyoung Seop Kim, the POSTECH team spent years studying HEAs. They used computer modeling and electron microscopy to fine-tune the alloy’s composition and L1₂ nanoparticle distribution. Adding cobalt and chromium enhanced thermal stability while keeping the alloy lightweight. Unlike a 2025 South Korean alloy (iron, aluminum, nickel) that was 10 times cheaper than titanium but brittle, the Hyperadaptor balances strength, ductility, and affordability.
Tests showed it withstands loads at −196°C, as in cryogenic chambers, and resists deformation at 600°C, as in turbines. Its tensile strength reaches 1.2 GPa, comparable to top titanium alloys but with superior temperature endurance.
Why Does It Matter?
Materials drive progress. The Hyperadaptor addresses a decades-old challenge: creating a metal that thrives in extreme conditions without compromising properties. This breakthrough:
- Accelerates Space Exploration: Lighter, cheaper rockets will aid Mars missions or asteroid mining.
- Reduces Emissions: More efficient turbines and engines will cut fuel consumption.
- Lowers Costs: Easier to process than titanium, it could reduce expenses in aviation and energy.
The global HEA market is projected to reach $2 billion by 2030, with the Hyperadaptor poised to lead. While China advances with 10G internet, South Korea counters with super materials, showcasing Asia’s innovation surge.
What’s Next?
POSTECH aims to scale Hyperadaptor production by 2027, starting with aerospace firms like Korea Aerospace Industries. Tests are underway at temperatures up to 800°C and in corrosive environments to broaden its applications. Plans include integrating it into 3D printing for complex parts. Competitors—Japan’s titanium-aluminum alloy (−269°C to 127°C) and the U.S.’s niobium alloy—are trailing, as the Korean material leads in temperature range.